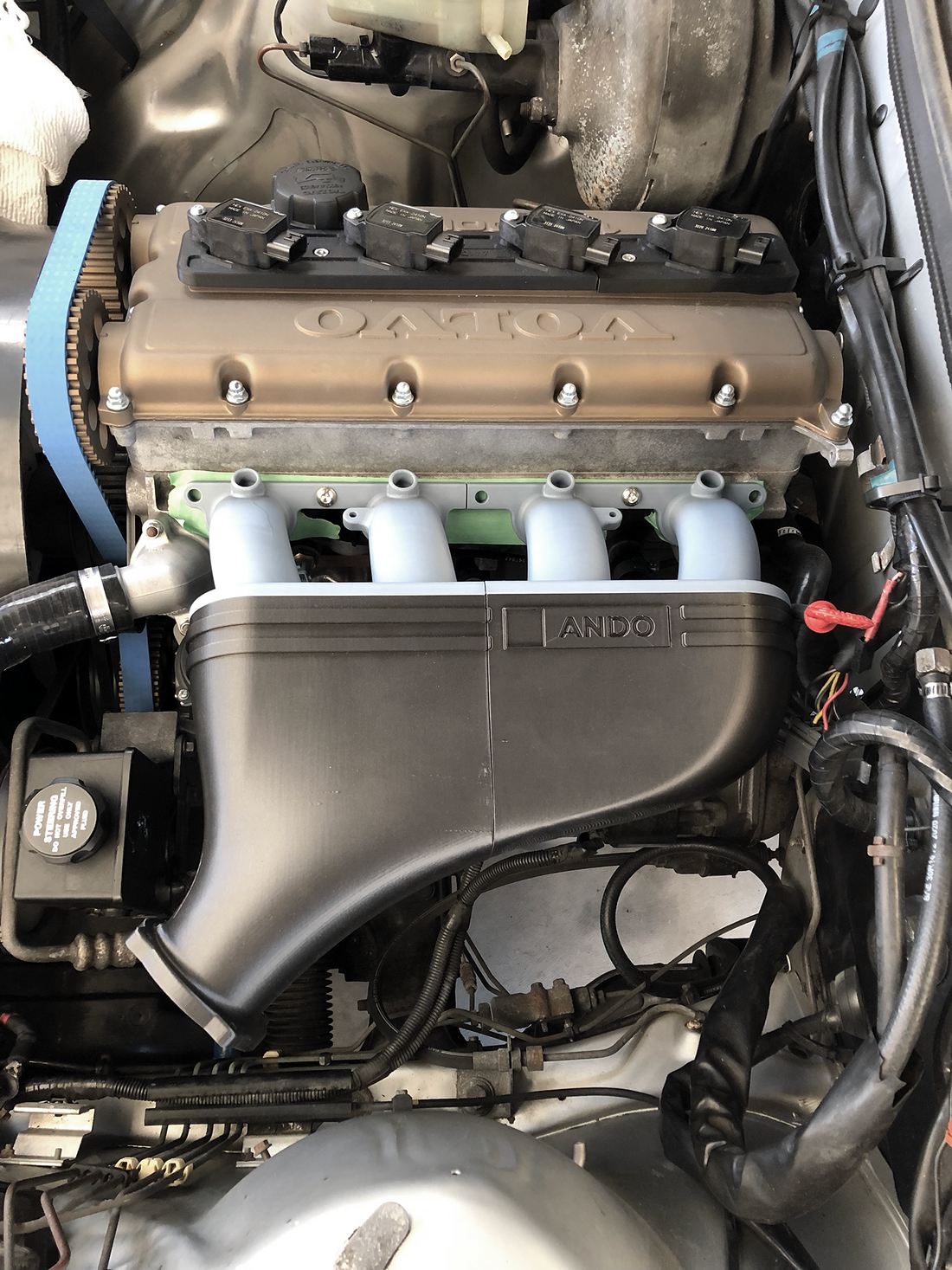
Intake Manifold Development
Share
Intake Manifold Design: Balancing Performance, Reliability, and Aesthetics
Before we began designing our intake manifold, we realized there were no options on the market reaching our expectations, especially compared to the more supported engines we’re accustomed to working with. Drawing on our experience in tuning engines, we identified several key features that we wanted to include for our design.
Key Features of Our Intake Manifold
Drive-by-Wire Throttle Body
A modern drive-by-wire throttle body was a must for our design. This eliminates the need for idle air control motors, which can complicate tuning and impact drivability if not done correctly, particularly for street cars where precision matters because we are not personally tuning every customers engine we wanted the most reliable result.
Many aftermarket throttle bodies are oversized, resulting in poor control during initial throttle openings. To strike the perfect balance, we chose the Bosch Motorsport 68mm drive-by-wire throttle. It’s cost-effective, reliable, and simplifies the manifold, we use a gasket-free, direct bolt-on fit using a Viton O-ring
Plenum Volume and Vacuum Porting
The plenum volume was carefully calculated to support performance while avoiding restrictions. From our research, plenum volume should be at least equal to the engine’s displacement, with some sources suggesting up to 150%. This gave us a solid starting point for design.
We also integrated functionality into the plenum by adding a brake booster port and hidden vacuum ports for the ECU and components like wastegates. These ports are tucked away for a clean look, out of sight and away from heat sources, with unused ports easily plugged using standard sized fittings.
Two-Piece Design for Serviceability
To enhance serviceability and improve internal flow design, we opted for a two-piece manifold, separating the plenum from the runners. This makes maintenance easier, as the plenum can be removed without disturbing the entire intake system.
For sealing, we avoided the common single O-ring design, which can be prone to leaks and damage. Instead, we used four individual Viton O-rings, one for each runner sourced from globally available suppliers. This design offers better durability and prevents boost pressure from creeping into bolt holes.
Another advantage of the two-piece design is the potential for future development. The plenum could be manufactured from alternative materials like carbon fibre or flax fibre using advanced 3D printing technologies. For our initial release, however, we’ve chosen high-quality cast aluminium to prioritize strength, temperature resistance, and reliability. We want our products to be trusted.
Runner Design and Fuel System
Our runners feature a bell mouth entry, commonly seen in individual throttle bodies, to smooth airflow and increase velocity. The runners are sized to eliminate restrictions, ensuring the cylinder head is the only limiting factor. The transition into the head was carefully designed to avoid angle changes, reducing turbulence and improving efficiency.
We can’t give away all the secrets, but we carefully calculated the runner length to maximize torque within the expected power band, taking full advantage of the strong bottom ends these engines are known for.
Injector placement was also optimized to ensure proper atomization into the intake charge. For the fuel rail, we chose a Nuke Performance rail, which is beautifully engineered and fits factory injector spacing. This ensures compatibility while maintaining a high-performance, clean setup. We tested the system using Injector Dynamics injectors, known for their excellent tuning data and reliability.
Form, Fit, and Future Possibilities
With functionality addressed, we turned our attention to aesthetics and fitment. By mounting the engine in the car during design, we ensured the manifold looked natural, with a vertical flange and horizontal appearance. This small detail makes a big difference in how the engine looks when installed.
The throttle body placement was carefully considered to avoid interference with the power steering pump, reservoir, strut tower, and ABS module. This allowed us to create a straight and level route for intercooler piping, and the space for fabricators to adapt custom pipework
We used 3D printing throughout the design process to confirm clearances and adjust details. This step allowed us to fine-tune the fitment and ensure all components worked together seamlessly. The result is a manifold that looks great, fits perfectly, and performs exceptionally.
Conclusion
Our intake manifold is a culmination of careful design, functionality, and aesthetics. From the modern drive-by-wire throttle body to the optimized plenum and runner designs, every detail was considered to ensure a high-performance, reliable product. We’re excited to share our dyno results and more technical insights in an upcoming blog post. stay tuned!